Power Quality is Vital in the Changing Commercial and Industrial Landscape
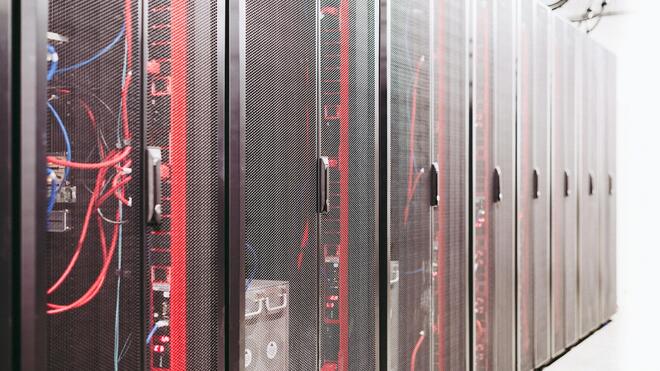
In the age of automation, EV infrastructure, and 24/7 cloud services, industrial and commercial operations demand more than just power—they demand precision. Power quality has become one of the most overlooked but costly vulnerabilities in today’s digital economy. A single voltage sag or transient, lasting only a few milliseconds, can disrupt robotic manufacturing lines, reset Programmable Logic Controllers (PLCs), corrupt data transfers, or delay mission-critical shipments. While utilities have made significant progress on reliability, the vast majority of power quality disturbances—voltage sags, transients, and harmonic distortion—originate inside the facility, not on the grid.
This truth has become increasingly evident as the grid evolves. Industries are shifting away from mechanical loads to highly sensitive electronic systems. EV chargers, inverters, variable frequency drives, and renewable systems now coexist within the same facility. These modern loads not only consume energy—they also interact with it in nonlinear, rapidly changing patterns that create new stresses on both the grid and the assets behind the meter. As a result, effective power quality monitoring is no longer optional—it's foundational to maintaining system performance.
According to a field study in Finland, something as seemingly simple as a wood splitter’s high inrush current caused significant voltage flicker and instability across the site, affecting other systems that shared the circuit. In another case from Texas, a medical facility’s imaging equipment caused voltage fluctuations that caused outages throughout the building due to faulty wiring.
These are not isolated incidents. A study by EPRI, cited by Rockwell Automation, found that industrial facilities experience an average of 66 voltage sags per year, costing U.S. businesses nearly $60 billion annually in downtime, equipment wear, and lost productivity. It’s a hidden cost that adds up quickly—and one that’s often avoidable with the right visibility and response tools in place.
Why Traditional Monitoring Isn’t Enough
Yet traditional monitoring tools still leave most of these events unseen. Fixed power quality meters typically sit at the customer premises, offering limited visibility and delayed insights, often taking two weeks for any analysis. They miss what’s happening deep inside the distribution grid, where disturbances affect productivity and safety the most. And interpreting that data often requires engineering expertise and scheduled reporting—leaving operations teams in the dark until it’s too late.
That’s when the UbiGrid® DTM+ comes into play. Installed at the last mile of the grid, these solutions transform distribution transformers into smart grid assets that continuously monitor both primary and secondary current and voltage. With a sampling rate of 130 times per cycle, they detect even subtle signs of trouble in real time—giving utilities and facility managers the visibility they need to prevent costly disruptions. This transformer-level approach bridges the gap in voltage monitoring solutions and allows for timely and precise detection of issues that traditional tools miss.
Real-Time Energy Analytics for Power Quality Visibility
Real-time visibility into power quality isn't just helpful—it's becoming essential. As loads become more dynamic and regulations more rigorous, facility and grid operators alike need better data to stay ahead. Ubicquia’s transformer-level monitoring integrates seamlessly with UbiVu® Analytics, providing intuitive dashboards and alerts that identify the source of disturbances, whether upstream from the grid or downstream within the facility. This helps operators not only diagnose but act—reducing truck rolls, accelerating root cause analysis, and building trust with commercial and industrial (C&I) customers.
In the case of the Texas medical facility, the local utility was able to utilize UbiGrid® DTM+ and UbiVu® Analytics to demonstrate to the facility operations team that the power quality issue was inside the building and not on the grid side. This visibility enabled the utility and the customer to collaborate on resolving the problem. This is an example of how real-time power grid analytics can improve communication, increase accountability, and shorten resolution times.
Adapting to New Loads and New Standards
This capability is becoming essential, not optional. The need to manage and maintain smart grid power quality has become a defining element of modern infrastructure planning. Smart grid compliance is now driven by updated regulatory expectations like IEEE 519-2022, which mandates strict harmonic distortion thresholds, and ANSI C84.1-2020, which defines allowable voltage variation limits. Compliance is no longer just about utility reliability—it’s about customer-side power quality that protects productivity and safeguards assets. This is especially critical as data centers, EV charging infrastructure, and on-site renewables place new demands on grid resilience. Facilities that once operated in isolation are now deeply connected to the edge, where performance and uptime hinge on the smallest electrical details.
The importance of modernizing edge infrastructure isn't limited to industrial settings. Cities are also rethinking how they manage essential services. In our blog Are You Still Driving Around Your City to Find Streetlights That Are Out? There’s a Better Way, we show how connected lighting can eliminate blind spots in maintenance. Similarly, Illuminating the Path to Public Safety explores how smart lighting networks are improving visibility, reducing crime, and supporting proactive safety strategies in both urban and rural communities.
Power Quality as a Business Priority
Addressing power quality today is not just a technical task—it’s a strategic advantage. With transformer-level monitoring in place, industrial operators can trace problems to specific circuits, avoid premature equipment failures, and collaborate with utilities to resolve issues before they escalate. Utilities, in turn, can better support their most demanding customers, reduce truck rolls, and enhance system reliability. As facilities embrace energy efficiency monitoring as part of their broader sustainability and reliability goals, investing in tools like the UbiGrid® DTM+ and UbiVu® becomes a key part of building resilient, intelligent infrastructure. These technologies are no longer futuristic—they’re essential tools for meeting the rigorous requirements of industrial power quality monitoring today and keeping pace with fast-changing future demands and grid modernization.